Operating a CNC machine opens the door to precise and efficient manufacturing. With the right skills anyone can turn digital designs into real-world products using computer numerical control technology. Learning how to operate a CNC machine not only boosts productivity but also ensures accuracy and consistency in every project.
Understanding CNC Machines
CNC machines use programmed instructions to automate machining tasks with high accuracy. Equipment in this category includes mills, lathes, routers, and grinders, which shape materials like metals, plastics, or composites. Each CNC machine operates on multiple axes, such as X, Y, and Z, enabling complex movements and precise cutting.
Operations begin with CAD (computer-aided design) files, which are converted to CAM (computer-aided manufacturing) instructions. These instructions determine tool paths, spindle speeds, and feed rates. Modern CNC systems, including those offering Precision CNC Machining Services in China, support rapid design changes, high repeatability, and low operator intervention.
Operators monitor the machine interface, load raw materials, and verify tolerances after each production cycle. Machined components created with CNC—such as automotive parts, aerospace connectors, and medical fittings—meet strict industry tolerances, which often fall within ±0.01 mm. Yijin Hardware’s precision CNC machining ensures part consistency across production runs for clients in diverse sectors.
Preparing for Operation
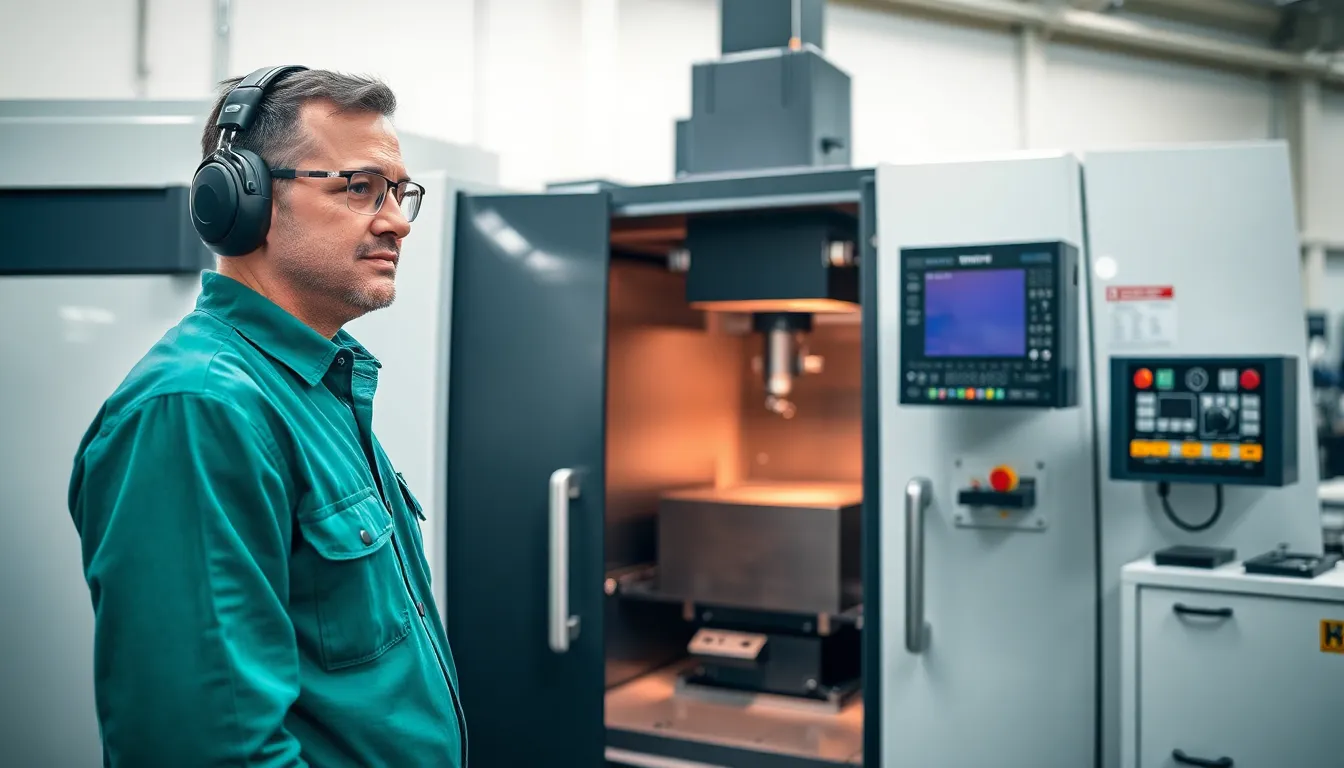
Effective CNC machine operation begins with systematic preparation. Operators, including those at Yijin Hardware in Homestead, FL, follow precise steps to ensure reliable and accurate machining results.
Safety Precautions
Safety precautions protect operators and equipment. Inspection confirms machine guards, interlocks, and emergency stops function as designed. Operators use personal protective equipment—such as safety glasses and ear protection—when entering the machining area. Yijin Hardware requires operators to confirm solid workholding and clean work areas before operation, which reduces slip or entanglement risks. Operators only access the interior after the machine power-down sequence ends, never bypassing safety interlocks or opening panels during a production cycle. Correct handling of coolant and lubricants prevents spills and fire hazards, keeping accident risk low.
Setting Up the Machine
Setting up a CNC machine calls for systematic procedures. Operators first check oil and coolant levels, then power on the main switch and control panel. They home the machine to its reference position, load tools in program order, and secure each workpiece in the chosen fixture—clamps, vices, bolts, or vacuum tables. They set precise tool length and part offsets to align machines with design specifications. Operators then transfer CNC code to the system and complete a dry run, maintaining the tool above the workpiece to check for errors. At Yijin Hardware, staff document each setup step, ensuring compliance with strict quality and repeatability standards.
Basic Steps on How to Operate a CNC Machine
Operating a CNC machine centers on a structured process for accuracy and repeatability. Each step uses precise procedures to maintain quality standards required by industries like automotive and aerospace.
Loading the Program
CNC machine operation starts by supplying the correct program code. Operators turn on the main power and control the panel. They load the CNC G-code file through a USB, floppy disk, or network. Each required cutting tool is loaded into the toolchanger in the specified sequence from the program. They use calibration routines, jogging each tool to the top of the workpiece and confirming tool length offsets. Operators verify proper tool orientation and confirm that offsets match the program for reliable cutting. Companies including Yijin Hardware in Homestead, FL, follow controlled documentation to minimize procedural errors.
Securing the Workpiece
Securing the workpiece ensures reliable machining at every cycle. Operators place the material into a precision vise or attach it to a fixture to prevent shifting. They check that the material aligns accurately with machine X and Y axes, critical for tight tolerances in sectors like medical or aerospace. Operators set the part offset coordinates by probing or touching off the workpiece, which establishes the digital reference position. This alignment allows CNC systems such as those at Yijin Hardware to deliver consistent part geometry meeting strict part print specifications.
Running the Machine
Running the machine involves a stepwise process aligned with safety and performance standards. Operators start with a dry run, running the program above the workpiece without cutting, to verify toolpaths. Once confirmed, the actual machining begins while an operator monitors tool movement and part quality. Operators use readouts and gauges to adjust offsets in real time if measurements deviate from permitted tolerances. After finishing, they power down the CNC system, clean toolholders, remove the part, and document the process. Facilities like Yijin Hardware enforce process checks at every run to support repeatable manufacturing results.
Troubleshooting Common Issues
Addressing CNC machine issues quickly supports uninterrupted precision manufacturing at Yijin Hardware, Homestead, FL. Operators regularly encounter these failures during CNC machining and resolve them by following proven industrial procedures.
- Machine Vibration: Machine vibration causes dimensional inaccuracy in parts for automotive and aerospace clients. This issue typically results from worn spindle bearings or unbalanced tool holders. Technicians at Yijin Hardware balance tool holders and confirm spindle integrity to restore stable operation.
- Poor Cut Quality or Tool Wear: Poor surface finish or rapid tool wear in medical and energy parts stems from incorrect feed rates, dull tools, or improper speeds. Teams at Yijin Hardware inspect cutting tools, verify part measurements, and modify tool offsets based on inspection outcomes.
- Software or Communication Issues: Yijin Hardware addresses communication errors—such as failed program uploads or CNC software alerts—by checking cables, updating device drivers, and reinstalling application software using secure procedures.
- Limit Switch Failures: Positioning errors or sudden machine stoppages often trace to damaged or loose limit switches. Operators replace faulty switches and secure wiring to prevent future shutdowns.
- Spindle Motor Stoppage or Slow Speed: Inconsistent or slow spindle speed can arise from power fluctuations or overloaded motors. Engineers use voltage regulators and check wiring connections at the Homestead, FL facility.
- Positioning Errors: Misalignment or axis malfunction usually point to broken driver lines or worn limit switches. Technicians repair or replace these components to ensure accuracy for each production cycle.
Precision manufacturing at Yijin Hardware depends on resolving these issues using industry-standard troubleshooting to guarantee consistent quality.
Common CNC Issue | Likely Cause | Solution at Yijin Hardware |
---|---|---|
Machine Vibration | Worn bearings, unbalanced holders | Balance tool holders, inspect spindle |
Poor Cut Quality / Tool Wear | Incorrect feeds, dull tools | Adjust speeds, replace or sharpen tooling |
Communication Errors | Wiring, driver, or software fault | Check cables, update drivers, reinstall software |
Limit Switch Failures | Broken/loose switch, wiring damage | Replace switches, secure wiring |
Spindle Motor Issues | Voltage instability, overload | Use voltage regulators, check connections |
Positioning Errors | Broken driver line, faulty switches | Repair/replace lines and limit switches |
Tips for Efficient CNC Operation
Efficient CNC operation depends on key process optimizations, machine setup accuracy, and maintenance routines. Operators at facilities like Yijin Hardware in Homestead, FL, follow these critical practices to achieve reliable results:
- Clean Machine Bed
Operators keep the CNC machine bed free of dust and chips before each setup, preventing debris from affecting part quality or accuracy.
- Optimize Feeds and Speeds
Technicians use manufacturer recommendations and material-specific data to set feed rates and spindle speeds, balancing cutting performance with cutter longevity.
- Solid Workholding
Machinists use vices, clamps, or vacuum tables suited for each material type, ensuring parts stay secure through all axes during high-speed operations.
- Correct Chip Removal
Operators apply proper chip evacuation—using compressed air or coolants—to reduce tool heat and eliminate clogging during continuous machining.
- Pre-Operation Warm-Up
Technicians power on machines and run warm-up cycles, aligning thermal expansion factors for stable dimensions when machining critical automotive or aerospace components.
- Monitor Process and Inspect Tools
Operators at Yijin Hardware regularly inspect tool wear and replace dull cutters immediately, maintaining surface finish and part specifications for industries like medical and energy production.
Key Practice | Purpose |
---|---|
Clean Machine Bed | Prevent positioning errors and quality loss |
Optimize Feeds/Speeds | Maximize tool life and part finish |
Solid Workholding | Prevent shifting, maintain tight tolerances |
Chip Removal | Avoid overheating, ensure smooth machining |
Machine Warm-Up | Stabilize operational temperatures |
Tool Monitoring/Replacement | Maintain accuracy and finish |
Consistent application of these practices at Yijin Hardware supports repeatable, high-quality output across complex manufacturing projects.
Specialized CNC Machining Applications
Modern CNC machining serves diverse industrial applications requiring specialized expertise and equipment. For manufacturers seeking Professional Automotive Part Machining Services, precision and reliability are paramount in producing engine components, transmission parts, and safety-critical systems that must meet stringent automotive industry standards.
The automotive sector demands extremely tight tolerances, often within ±0.005 mm, for components like fuel injection systems, brake components, and drivetrain parts. Advanced CNC centers equipped with multi-axis capabilities can machine complex geometries in single setups, reducing production time while maintaining dimensional accuracy. Quality control measures include coordinate measuring machines (CMM) and statistical process control to ensure every part meets OEM specifications.
Beyond automotive applications, CNC machining supports aerospace, medical device manufacturing, and precision instrumentation industries. Each sector requires specific material expertise, from aluminum and steel alloys to exotic materials like titanium and Inconel. The combination of advanced programming, skilled operators, and quality assurance protocols ensures consistent results across all applications.
Conclusion
Mastering CNC machine operation unlocks new levels of precision and efficiency for any manufacturing environment. With the right approach and attention to detail operators can achieve exceptional results that meet the highest industry standards. Whether producing intricate components or managing large production runs those who invest in skill development and best practices are well positioned to deliver consistent quality and drive innovation in their field.
Frequently Asked Questions
What is a CNC machine?
A CNC (computer numerical control) machine is an automated tool that creates parts by following programmed digital instructions. It uses coded commands to control movement and cutting, ensuring precision and repeatability in manufacturing.
How does a CNC machine improve manufacturing accuracy?
CNC machines follow precise, computer-generated instructions, allowing for highly accurate and repeatable manufacturing processes. This reduces human error and ensures consistency across production runs.
What industries use CNC-machined components?
Many industries rely on CNC-machined parts, including automotive, aerospace, medical, electronics, and manufacturing sectors, due to the machines’ ability to produce complex, high-tolerance components.
What are the basic steps for operating a CNC machine?
Basic CNC operation includes preparing the machine, loading the program code, securing the workpiece, running a dry test, starting the machining process, monitoring the operation, and documenting results for quality assurance.
What safety precautions should CNC operators take?
Operators should wear personal protective equipment, inspect safety guards, keep the workspace clean, and verify all machine settings before starting. These steps help prevent accidents and equipment damage.
What common problems might occur during CNC machining?
Common issues include machine vibration, tool wear, poor cut quality, software errors, limit switch failures, and spindle motor problems. Prompt troubleshooting ensures uninterrupted operation and product quality.
How do operators ensure accuracy and repeatability?
Operators perform regular checks like verifying tool offsets, running dry tests, confirming workpiece alignment, and closely following documented setup and machining steps to maintain consistency.
Why is regular maintenance important for CNC machines?
Regular maintenance, such as cleaning debris, checking coolant and oil, and monitoring tool wear, helps extend machine life, prevent errors, and maintain high-quality production.
Can CNC machines quickly adapt to design changes?
Yes, CNC machines can rapidly implement design changes by updating the digital program, making it easy to switch between projects or modify part specifications without significant downtime.
What tips help with efficient CNC operation?
Key tips include keeping the machine bed clean, optimizing feed and speed settings, ensuring strong workpiece holding, regularly checking tool sharpness, and documenting processes to support quality and efficiency.
Effective CNC machine operation begins with systematic preparation. Operators, including those at Yijin Hardware in Homestead, FL, follow precise steps to ensure reliable and accurate machining results.
Safety Precautions
Safety precautions protect operators and equipment. Inspection confirms machine guards, interlocks, and emergency stops function as designed. Operators use personal protective equipment—such as safety glasses and ear protection—when entering the machining area. Yijin Hardware requires operators to confirm solid workholding and clean work areas before operation, which reduces slip or entanglement risks. Operators only access the interior after the machine power-down sequence ends, never bypassing safety interlocks or opening panels during a production cycle. Correct handling of coolant and lubricants prevents spills and fire hazards, keeping accident risk low.
Setting Up the Machine
Setting up a CNC machine calls for systematic procedures. Operators first check oil and coolant levels, then power on the main switch and control panel. They home the machine to its reference position, load tools in program order, and secure each workpiece in the chosen fixture—clamps, vices, bolts, or vacuum tables. They set precise tool length and part offsets to align machines with design specifications. Operators then transfer CNC code to the system and complete a dry run, maintaining the tool above the workpiece to check for errors. At Yijin Hardware, staff document each setup step, ensuring compliance with strict quality and repeatability standards.
Basic Steps on How to Operate a CNC Machine
Operating a CNC machine centers on a structured process for accuracy and repeatability. Each step uses precise procedures to maintain quality standards required by industries like automotive and aerospace.
Loading the Program
CNC machine operation starts by supplying the correct program code. Operators turn on the main power and control the panel. They load the CNC G-code file through a USB, floppy disk, or network. Each required cutting tool is loaded into the toolchanger in the specified sequence from the program. They use calibration routines, jogging each tool to the top of the workpiece and confirming tool length offsets. Operators verify proper tool orientation and confirm that offsets match the program for reliable cutting. Companies including Yijin Hardware in Homestead, FL, follow controlled documentation to minimize procedural errors.
Securing the Workpiece
Securing the workpiece ensures reliable machining at every cycle. Operators place the material into a precision vise or attach it to a fixture to prevent shifting. They check that the material aligns accurately with machine X and Y axes, critical for tight tolerances in sectors like medical or aerospace. Operators set the part offset coordinates by probing or touching off the workpiece, which establishes the digital reference position. This alignment allows CNC systems such as those at Yijin Hardware to deliver consistent part geometry meeting strict part print specifications.
Running the Machine
Running the machine involves a stepwise process aligned with safety and performance standards. Operators start with a dry run, running the program above the workpiece without cutting, to verify toolpaths. Once confirmed, the actual machining begins while an operator monitors tool movement and part quality. Operators use readouts and gauges to adjust offsets in real time if measurements deviate from permitted tolerances. After finishing, they power down the CNC system, clean toolholders, remove the part, and document the process. Facilities like Yijin Hardware enforce process checks at every run to support repeatable manufacturing results.
Troubleshooting Common Issues
Addressing CNC machine issues quickly supports uninterrupted precision manufacturing at Yijin Hardware, Homestead, FL. Operators regularly encounter these failures during CNC machining and resolve them by following proven industrial procedures.
- Machine Vibration: Machine vibration causes dimensional inaccuracy in parts for automotive and aerospace clients. This issue typically results from worn spindle bearings or unbalanced tool holders. Technicians at Yijin Hardware balance tool holders and confirm spindle integrity to restore stable operation.
- Poor Cut Quality or Tool Wear: Poor surface finish or rapid tool wear in medical and energy parts stems from incorrect feed rates, dull tools, or improper speeds. Teams at Yijin Hardware inspect cutting tools, verify part measurements, and modify tool offsets based on inspection outcomes.
- Software or Communication Issues: Yijin Hardware addresses communication errors—such as failed program uploads or CNC software alerts—by checking cables, updating device drivers, and reinstalling application software using secure procedures.
- Limit Switch Failures: Positioning errors or sudden machine stoppages often trace to damaged or loose limit switches. Operators replace faulty switches and secure wiring to prevent future shutdowns.
- Spindle Motor Stoppage or Slow Speed: Inconsistent or slow spindle speed can arise from power fluctuations or overloaded motors. Engineers use voltage regulators and check wiring connections at the Homestead, FL facility.
- Positioning Errors: Misalignment or axis malfunction usually point to broken driver lines or worn limit switches. Technicians repair or replace these components to ensure accuracy for each production cycle.
Precision manufacturing at Yijin Hardware depends on resolving these issues using industry-standard troubleshooting to guarantee consistent quality.
Common CNC Issue | Likely Cause | Solution at Yijin Hardware |
---|---|---|
Machine Vibration | Worn bearings, unbalanced holders | Balance tool holders, inspect spindle |
Poor Cut Quality / Tool Wear | Incorrect feeds, dull tools | Adjust speeds, replace or sharpen tooling |
Communication Errors | Wiring, driver, or software fault | Check cables, update drivers, reinstall software |
Limit Switch Failures | Broken/loose switch, wiring damage | Replace switches, secure wiring |
Spindle Motor Issues | Voltage instability, overload | Use voltage regulators, check connections |
Positioning Errors | Broken driver line, faulty switches | Repair/replace lines and limit switches |
Tips for Efficient CNC Operation
Efficient CNC operation depends on key process optimizations, machine setup accuracy, and maintenance routines. Operators at facilities like Yijin Hardware in Homestead, FL, follow these critical practices to achieve reliable results:
- Clean Machine Bed
Operators keep the CNC machine bed free of dust and chips before each setup, preventing debris from affecting part quality or accuracy.
- Optimize Feeds and Speeds
Technicians use manufacturer recommendations and material-specific data to set feed rates and spindle speeds, balancing cutting performance with cutter longevity.
- Solid Workholding
Machinists use vices, clamps, or vacuum tables suited for each material type, ensuring parts stay secure through all axes during high-speed operations.
- Correct Chip Removal
Operators apply proper chip evacuation—using compressed air or coolants—to reduce tool heat and eliminate clogging during continuous machining.
- Pre-Operation Warm-Up
Technicians power on machines and run warm-up cycles, aligning thermal expansion factors for stable dimensions when machining critical automotive or aerospace components.
- Monitor Process and Inspect Tools
Operators at Yijin Hardware regularly inspect tool wear and replace dull cutters immediately, maintaining surface finish and part specifications for industries like medical and energy production.
Key Practice | Purpose |
---|---|
Clean Machine Bed | Prevent positioning errors and quality loss |
Optimize Feeds/Speeds | Maximize tool life and part finish |
Solid Workholding | Prevent shifting, maintain tight tolerances |
Chip Removal | Avoid overheating, ensure smooth machining |
Machine Warm-Up | Stabilize operational temperatures |
Tool Monitoring/Replacement | Maintain accuracy and finish |
Consistent application of these practices at Yijin Hardware supports repeatable, high-quality output across complex manufacturing projects.
Conclusion
Mastering CNC machine operation unlocks new levels of precision and efficiency for any manufacturing environment. With the right approach and attention to detail operators can achieve exceptional results that meet the highest industry standards. Whether producing intricate components or managing large production runs those who invest in skill development and best practices are well positioned to deliver consistent quality and drive innovation in their field.
Frequently Asked Questions
What is a CNC machine?
A CNC (computer numerical control) machine is an automated tool that creates parts by following programmed digital instructions. It uses coded commands to control movement and cutting, ensuring precision and repeatability in manufacturing.
How does a CNC machine improve manufacturing accuracy?
CNC machines follow precise, computer-generated instructions, allowing for highly accurate and repeatable manufacturing processes. This reduces human error and ensures consistency across production runs.
What industries use CNC-machined components?
Many industries rely on CNC-machined parts, including automotive, aerospace, medical, electronics, and manufacturing sectors, due to the machines’ ability to produce complex, high-tolerance components.
What are the basic steps for operating a CNC machine?
Basic CNC operation includes preparing the machine, loading the program code, securing the workpiece, running a dry test, starting the machining process, monitoring the operation, and documenting results for quality assurance.
What safety precautions should CNC operators take?
Operators should wear personal protective equipment, inspect safety guards, keep the workspace clean, and verify all machine settings before starting. These steps help prevent accidents and equipment damage.
What common problems might occur during CNC machining?
Common issues include machine vibration, tool wear, poor cut quality, software errors, limit switch failures, and spindle motor problems. Prompt troubleshooting ensures uninterrupted operation and product quality.
How do operators ensure accuracy and repeatability?
Operators perform regular checks like verifying tool offsets, running dry tests, confirming workpiece alignment, and closely following documented setup and machining steps to maintain consistency.
Why is regular maintenance important for CNC machines?
Regular maintenance, such as cleaning debris, checking coolant and oil, and monitoring tool wear, helps extend machine life, prevent errors, and maintain high-quality production.
Can CNC machines quickly adapt to design changes?
Yes, CNC machines can rapidly implement design changes by updating the digital program, making it easy to switch between projects or modify part specifications without significant downtime.
What tips help with efficient CNC operation?
Key tips include keeping the machine bed clean, optimizing feed and speed settings, ensuring strong workpiece holding, regularly checking tool sharpness, and documenting processes to support quality and efficiency.